08-16-2023
Two technologies in one system: WINTERSTEIGER offers an overall concept for cleaning and repairing wood surfaces
On the production line consisting of a TRC Preclean with four modules for precleaning wooden boards and two TRC Panel 3TH systems for repairing defects, all processing steps run fully automatically. Secondary processes such as unloading, loading, scanning, and evaluating take place while defects are being machined. With this combi system, WINTERSTEIGER aims for the best possible material flow.
Precleaning: Natural contours are preserved.
In the first step, the planks are cleaned with the automatic TRC Preclean. Soft and loose damaged parts are removed during this process.
The special feature of the TRC Preclean is that the natural contours of the defects are preserved. This is where the defect scanner developed by WINTERSTEIGER comes into play. It precisely measures the defect and, depending on the size and geometry of the defect, the milling tool is then selected that precisely follows the contour of the defect in several axes. Further advantages of automatic cleaning are the consistent quality of the results and the improved workplace safety. Employees no longer have to work with compressed air milling cutters or the like.
The fully automated TRC Preclean is designed to be modular and is available in several configurations.
SHARE:
Repair: Measure defects precisely.
After cleaning, the planks are repaired in the fully automated TRC Panel timber repair system. The system processes several planks in layers and not individual planks, i.e., the planks are connected to each other on one layer.
A key element of each system is the 3D scanner developed in-house. The evaluation of defects is not carried out using database comparisons of patterns, but instead all defects are recalculated for each board. The scanner detects defects from a size of 0.5 mm (knothole diameter, crack width, etc.) and the scanner works at a speed of approximately 72 m/minute. Thanks to the unique WINTERSTEIGER software, the injection heads quickly approach the identified defects and process them precisely.
Automated repair: What are the advantages?
The main advantages include high savings in filling material and labor. In addition, the use of TRC systems leads to a sustainable improvement in quality, as manual surface repair is heavily dependent on the skill of the employee in question and differences are compensated for with automation. Air inclusions that can occur during manual repairs are avoided with the TRC system. The special injection process also means that the filling material holds better in the defect.
The unique feature of TRC: Two filling materials to choose from.
A key issue during processing is the drying time. WINTERSTEIGER systems offer flexibility here with two filling materials to choose from:
- The thermoplastic filling material (TH) hardens immediately after the filling process: the temperature is cooled with a cooling plate and the material can be processed immediately. Filling and cooling are carried out in one step.
- The organic filling material (OR) is incorporated when cold and must be allowed to dry out. The duration depends on the size of the defect, i.e., the volume of the inserted material and the thickness of the top layer. It can take up to 12 hours.
There are different colors of filling material, with customized colors possible in addition to the standard colors.
Systems for every requirement.
The TRC systems are mainly used in the production of parquet flooring, but are also in demand in the furniture and panel industry – several projects have already been realized for these industries. In terms of capacity, WINTERSTEIGER provides systems for a wide range of companies: for micro-enterprises with a volume of 50,000 m2 of parquet floors per year to industrial enterprises with more than one million m2. Some of the systems are modular and can be expanded according to capacity requirements.
Different machine platforms and two technologies for the filling material: depending on the requirements, WINTERSTEIGER puts together the right concept for each individual customer.
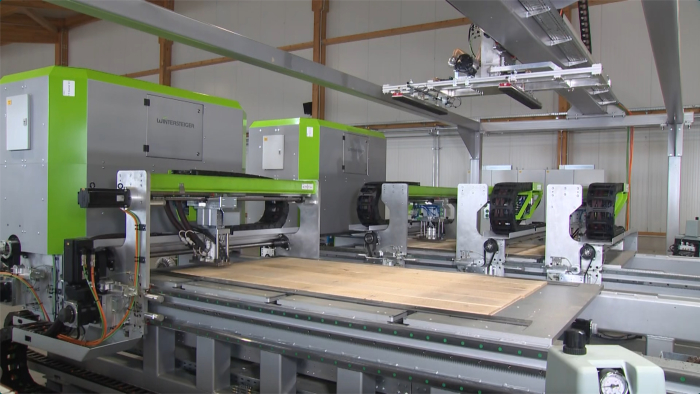
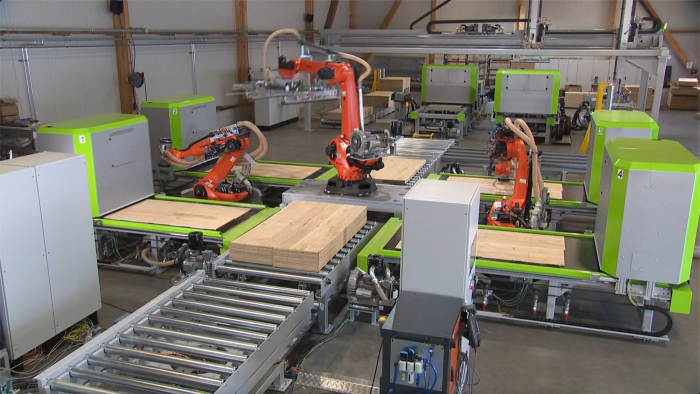