26.04.2016
Give me five! 5 automated ski servicing machines for Bründl Sports
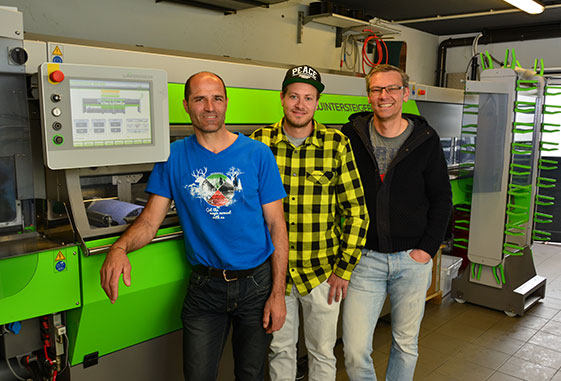
Bründl Sports of Austria purchased its first Discovery 10 years ago. This year, it has really gone all out and ordered a Discovery each for the mountain and valley stations of the new Penken cableway in Mayrhofen, as well as one each for its Waidmannsheil branch in Kaprun, its branch in Schladming and its designer outlet in Salzburg. In an interview, Herbert Neumayer, a member of Bründl Sports' management, and heads of race ski servicing Hans Hofer and Lukas Wallner spoke about what they expect from an automated ski servicing machine.
WINTERSTEIGER: Mr. Neumayer, from the management's perspective, what matters to you when it comes to an automated ski servicing machine?
Herbert Neumayer: As the name indicates, it is an automated machine. It should do its work without me having to provide two people to "supervise" it. We need a reliable, stable machine. I also expect an automated ski servicing machine to be easy to operate. A seasonal employee must be able to learn how to use it quickly and achieve the same results as an experienced staff member. Another issue is cost-effectiveness. In our workshops, we grind about 73,000 pairs of skis on WINTERSTEIGER machines each year, two thirds of them being rental skis. If the basic functions of a machine don't work properly, the results won't be right either.
WINTERSTEIGER: Mr. Hofer, you have been a professional ski racer, have worked in race ski development at Blizzard, were the head of the women's race ski department at Fischer and have also worked at the ÖSV (Austrian Ski Association) Skiing Competence Center. Now you are head of race ski servicing at Bründl. How much importance is given to race ski servicing at Bründl?
Hans Hofer: Lukas and I have been servicing race skis for 6 years and it has developed very well. Ski racers from countries like Australia, Lithuania, England and Spain – basically any country where they have no place of their own to go to – now come to us for our expertise.
WINTERSTEIGER: Your wealth of technical knowledge has also been of benefit to WINTERSTEIGER: The new Discovery with the stone, disc, stone and polishing modules at your Waidmannsheil branch was built according to your requirements. What makes it special?
Hans Hofer: There is quite a bit that we developed together. Clamping cylinders that yield flexibly are one example. The ski is kept nice and flat as it is fed through the machine. Our machine no longer grinds islands at the ski tips, because the cylinders are not stiff, but function like shock absorbers. As a result, we are even able to grind wide ski tips very nicely.
The new polishing module makes it possible for the tails and tips of both regular customer skis and race skis to be processed perfectly, which is very important for maneuverability. We were able to provide some valuable information here, too.
Lukas Wallner: We adjust the grinding angle of the disc module on our Discovery electronically. That means that we no longer need to stop the machine to open the access hatch. We no longer need to reach into the wet machine and the angle is adjusted in less than 5 seconds. That makes our work much easier. The edge geometry is even more precise and the discs remove material much more evenly.
The "paternoster lift" ski magazine system is also extremely important to us. We can continue working on race skis manually as soon as it is loaded.
WINTERSTEIGER: Bründl is known for providing its customers with top-quality service. How do you find being on the receiving of WINTERSTEIGER's service?
Herbert Neumayer: WINTERSTEIGER is distinguished by service! When we need help, someone is there very quickly. We also take advantage of the remote maintenance service, where we can get the assistance we need easily and efficiently.
WINTERSTEIGER: Thank you very much for the interesting interview!
SHARE: