22.06.2020
Discovery with 5 modules: A successful ski service – even away from ski resorts
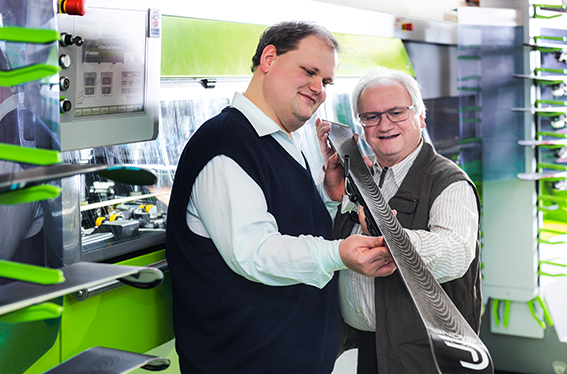
© Klemens Klinger
Where is the largest automated ski service machine in Upper Austria? At Sport Hochleithner in Bad Wimsbach, a community with barely 2,500 residents, about 50 km from the next major ski resort. The recipe for success for forward-looking entrepreneurs? A heightened awareness of quality and a lot of attention to detail, seasoned with personal commitment.
Alfred Hochleithner and his son, who will soon be the fourth generation of his family to run the business, replaced the automated Finish Shuttle 3C with a Discovery 2 with 5 modules: Stone, Disc, Stone, Disc, and Finish. Sports retailers are excited about the new, powerful machine, which allows them to quickly create more throughput and also to achieve perfect service results. Seamless grinding and a ski magazine for 16 skis save time and effort.
Alfred Hochleithner considers the machine's electronic angle adjustment to be a real bonus: it allows him to respond quickly and effortlessly to different customer requirements, and thanks to the disc technology, the edge is ground as precisely as in racing. With 2 Stone modules for pregrinding and fine grinding, the machine can achieve any structural pattern for a wide variety of snow conditions. According to the experts, the wave structure is ideal for all conditions at present and is currently the Sport Hochleithner trademark. Their customers regularly voice their enthusiasm for the structure, with one skier even commenting: "The skis are so beautiful, it's almost a shame to use them!"
SHARE:
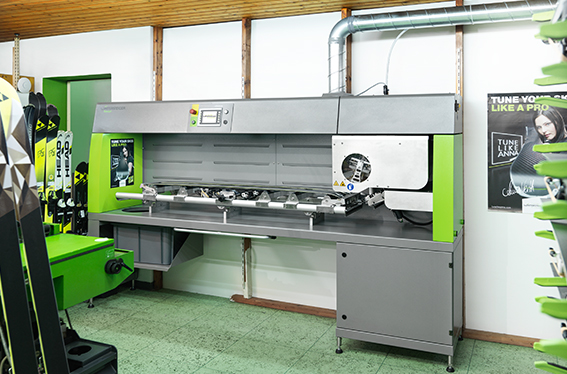
© Klemens Klinger
Systematic binding checks.
Sports Hochleithner has 2 devices for checking and adjusting bindings, so that father and son do not get in each other's way when working. Every customer gets a clearly visible sticker on their skis with the test date, to remind them when the next check is due. "It's not a bad thing to check that a system is working, even if it is maintenance-free," says Alfred Hochleithner Junior, who has a second job as a trained IT specialist. Customers are keen to get this done and most of them have the check carried out on an annual basis.
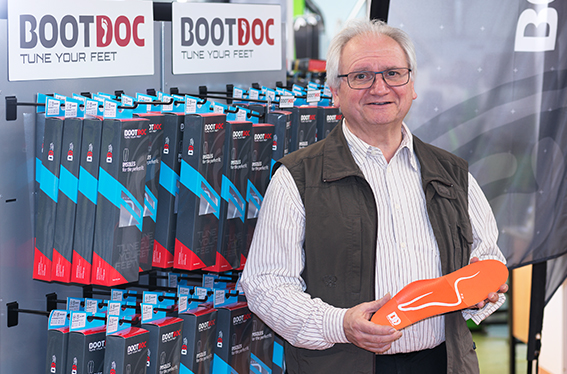
© Klemens Klinger
BOOTDOC insoles also play a role.
BOOTDOC insoles are another successful product for the Hochleithner family, and are included in the sale of more than 80 % of ski boots, as well as hiking boots, running shoes, and work shoes. Alfred Hochleithner Senior, who was originally a bootmaker, is convinced that every foot needs perfect bedding. Sport Hochleithner is now famous for finding solutions to foot problems.