12.04.2022
Wibeba-Holz automates furniture panel repair
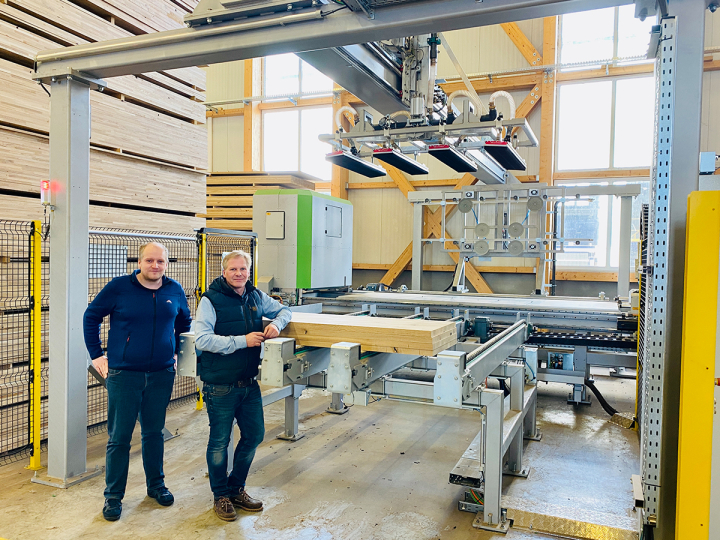
VAP-WINTERSTEIGER Delivers a System for the Repair of Large Panels
At Wibeba-Holz in Wieselburg, the TRC Panel 2000 has been brought in to handle furniture panel repairs fully automatically, on both sides, and with large panel dimensions. The new TRC system can lift weights of up to 150 kg. This makes panel handling considerably easier and frees up valuable personnel resources for other tasks. Perfectly tailored to the company requirements, the system repairs 60,000 m2 per year, primarily oak.
The TRC Panel 2000 was developed for Wibeba-Holz – with a little detour, explains Wibeba CEO Wolfgang: “When looking for a way to automate our repair processes, I came across VAP-WINTERSTEIGER. Originally, the scanner did not have the capacity to scan panel widths of 1300 mm and so at first we pursued a semi-automatic solution. Over the course of our cooperation, VAP-WINTERSTEIGER was able to develop a solution for these panel dimensions. The new system is perfectly tailored to our requirements.” Despite the panel size – with lengths up to 3 m and widths up to 1.25 m – the TRC Panel 2000 is a highly compact system. It features a turning unit and repairs the panels on both sides: After scanning and repairing the front, the vacuum gripper turns the panel 180 degrees in order to process the back.
SHARE:
More quality, less filling material.
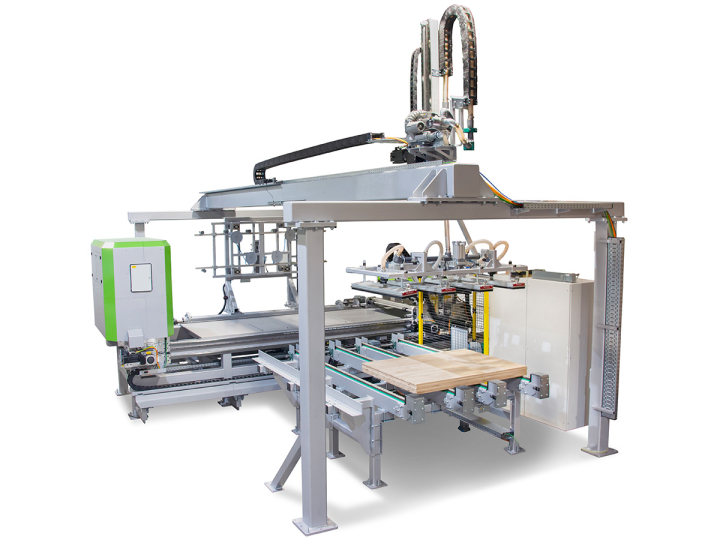
More quality, less filling material.
When asked what the main benefits of the new system were, Wolfgang Sunk answered: “The accuracy of the scanner, i.e. defect detection, and the quality of the repairs are both excellent. The system works around the clock with unwavering precision, which means the quality always remains constant.” The automated system also freed up valuable personnel resources: “The TRC system works fully automatically, and we were able to reshuffle our work processes. We used to have 2–3 employees assigned to filling,” Sunk reports. Alongside personnel resources, filling material savings are another bonus: “Previously, at least 50% too much filling material was applied,” Wolfgang Sunk estimates with regard to material wastage. With the TRC system, the defect scanner precisely measures the affected area and calculates the amount of filling material – this exact volume is then injected into the defect at high pressure and high precision.
The high standard of quality is one of the constants in the success of Wibeba-Holz, alongside availability and the ability to deliver. “It is essential that customers are able to rely on a company long term, and we prove that every day,” explains Wolfgang Sunk with regard to his view on the future of the wood processing industry.
About Wibeba-Holz.
Wibeba-Holz is considered to be Austria’s hardwood specialist. The family business produces sawn timber, solid wood panels, door frame wood, and parquet elements for the furniture and door industry as well as the wood trade at 5 company locations in Austria and Hungary. They work with oak, Hungarian black walnut, acacia, beech, alder, ash, and maple.
- Employees: 150, 55 of which in Wieselburg
- 5 sites: Wieselburg (headquarters and solid wood board production), Güssing (drying and logistics center), Heiligenkreuz (solid wood board production), Rönök, and Szenta (sawmills) in Hungary
- Annual cutting output: 60,000 solid cubic meters of European hardwood
- Laminated panel mill in Wieselburg: 330,000 m² per year
- Export percentage: 75%, primary markets: Germany, Switzerland, and Asia
- www.wibeba-holz.com