17.10.2022
Esco CZ Productions: TRC technology brings completely new production processes
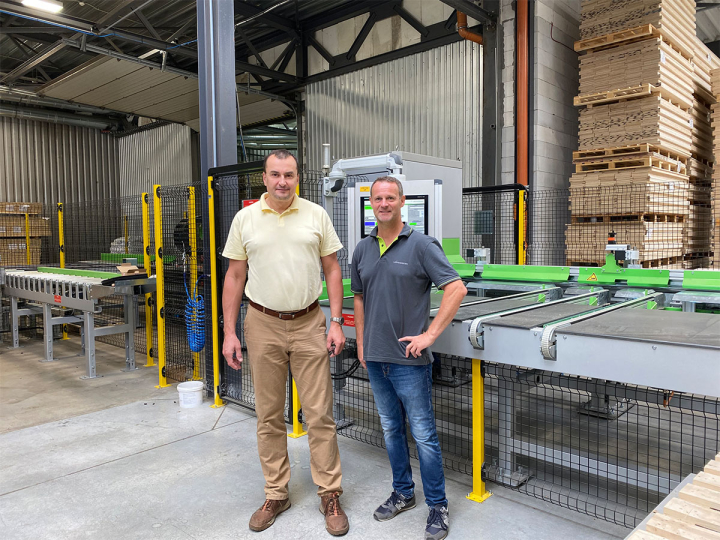
© WINTERSTEIGER
Two TRC 1500 systems repair 400,000 m2 per year
Radek Votápek, Operations Manager of Esco CZ Productions, prefers smart solutions. In the search for an automated solution for the cleaning of wooden lamellae, he came across WINTERSTEIGER and initially ordered two fully automated TRC 1500 systems for timber surface repair.
Mr. Votápek explains the decision-making process: “Our main concern was expanding and stabilizing the capacity for timber repair without increasing the number of employees.”
Important changes in the production process.
With the new TRC 1500 systems, Esco is repositioning 90 % of the machines and the production process will change completely. Following completion of the new production building with an area of 3,200 m2, the company will be in a position to produce a larger volume with reduced logistics costs and lower labor costs per unit.
The capacity of the TRC systems is heavily dependent on the quality of the lamellae. Together with WINTERSTEIGER, Esco has performed tests, the results of which show that Esco can process 600–700 m2 at its average quality level on each TRC system per 8-hour shift. This results in more than 400,000 m2 of repaired flooring per year, assuming 12-hour operation for each system.
SHARE:
Further benefits.
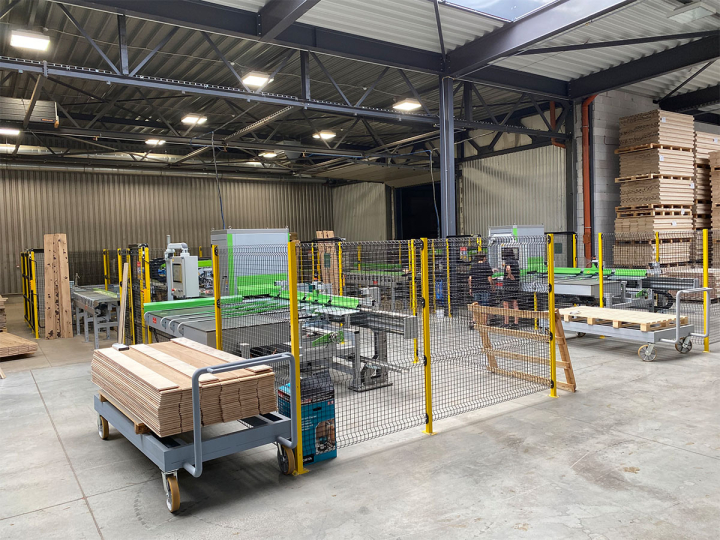
© WINTERSTEIGER
For Esco, there is one main advantage of TRC technology: repaired lamellae can be immediately transported onwards to the next production step without delays due to stacking, drying, etc. This reduces stock levels and provides a better overview of the entire process.
Another plus is that initial tests have shown that the repair of larger knotholes has an improved appearance compared to manual filling, because the surface is finer after brushing and the defect is more compact.
Esco is also anticipating a sustainable increase in quality and performance. Manual surface repair is heavily dependent on the skill of the employees and the training time is highly variable. Automation compensates for this.
Special feature: Two colors in one machine.
One of the TRC machines works with two colors. This option allows the company to remain very flexible: Esco produces the entire order volume made to order, so flexibility and short setup times are important due to small production volumes.
Valuable raw material.
“We see the efficient use of oak as our responsibility toward nature and toward ourselves. Oak has never been more expensive, and for those that understand the need to get the most out of it, it brings fantastic business advantages,” says Radek Voltápek. Each individual oak log is checked by Esco employees in the company forest before it is delivered. Esco has its own sawmill, in which all the oak and lamellae are produced. “The entire process is performed in-house, from the oak forest to the finished flooring, and all under our control. We thoroughly enjoy it.”
About Esco
Esco CZ Production is a family-run (originally Dutch) company with two sites in the Czech Republic. Sixty percent is owned by a Dutch family (Mr. and Ms. Kuijpers), 40 % belongs to Belgian company Decospan NV through its association The Veneer NV.
Employees: | 160 |
Production: | 360,000 m2 of oak flooring per year |
Target group: | Luxury wholesalers, construction companies, architects and designers, investors, and specialized flooring installers |
Sales: |
14.2 million euros |
Total production area: |
approx. 15,000 m2 |
Export ratio: |
65 %, global sales network |