06.02.2024
Precise and efficient sawing of lightweight core materials
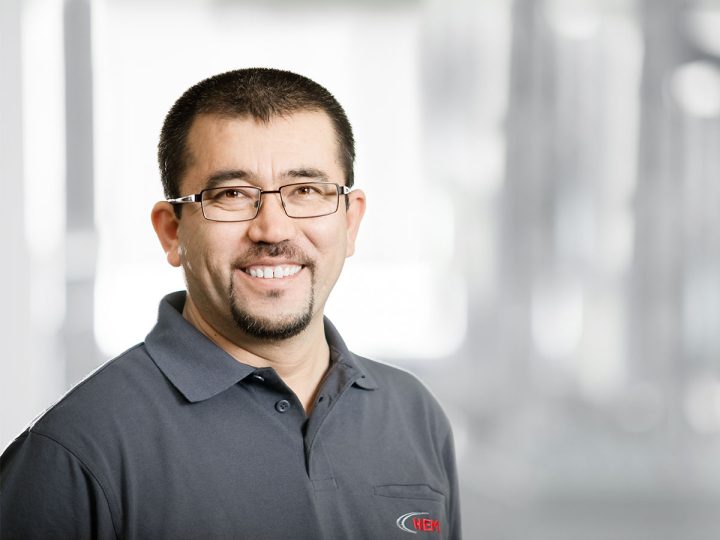
Heermann Maschinenbau GmbH
In the light of the goal of reducing CO2 emissions and energy consumption in conjunction with growing mobility, the demand for lighter and simultaneously more robust materials is constantly increasing. Lightweight core materials play a central role in meeting this demand. The proportion of these core materials is increasing in many industries, especially in sectors such as aerospace, transport vehicles and wind power. Processing these high-value core materials requires special cutting technologies to achieve maximum precision with minimal material loss.
Honeycomb core materials, such as aramid, aluminium, and fibreglass, are used in areas such as interiors, winglets, spoilers and many other parts in commercial and military aircraft, helicopters and similar.
The rotor blades of wind turbines are becoming ever larger to increase energy efficiency. This places higher demands on lightweight materials. Rotor blade core materials include (recycled) PET, PVC rigid foams, balsa wood and others.
Rigid foam panels (e.g. PET, PU) and honeycomb structures (e.g. PP) are used in transport vehicles, trains and ships to form interior fittings, side walls, roofs, floors, partitions, sanitary fixtures, etc.
Typically, these lightweight core materials are further processed into a form of sandwich panel structure by reinforcing them with glass or carbon fibres, for example, to increase their stiffness.
SHARE:
Using lightweight core materials – example applications
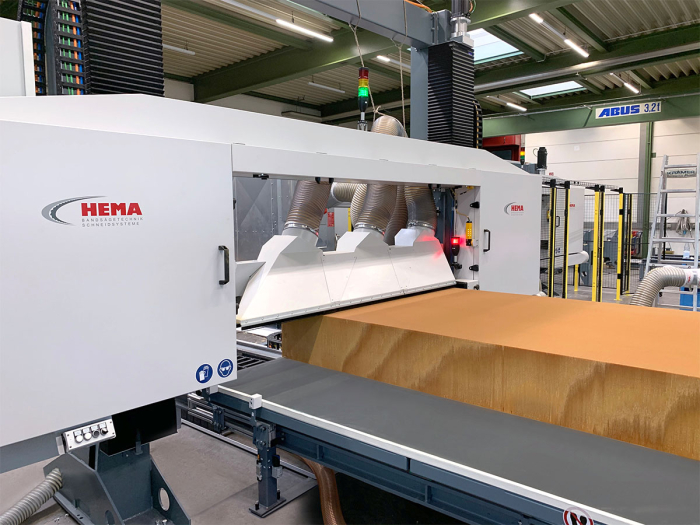
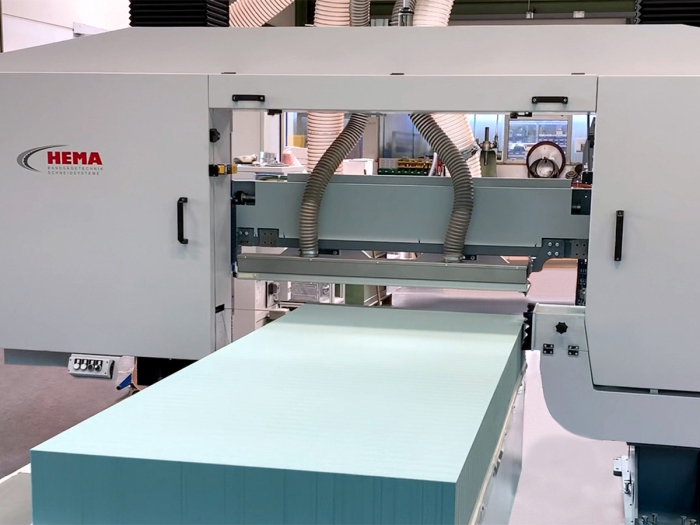
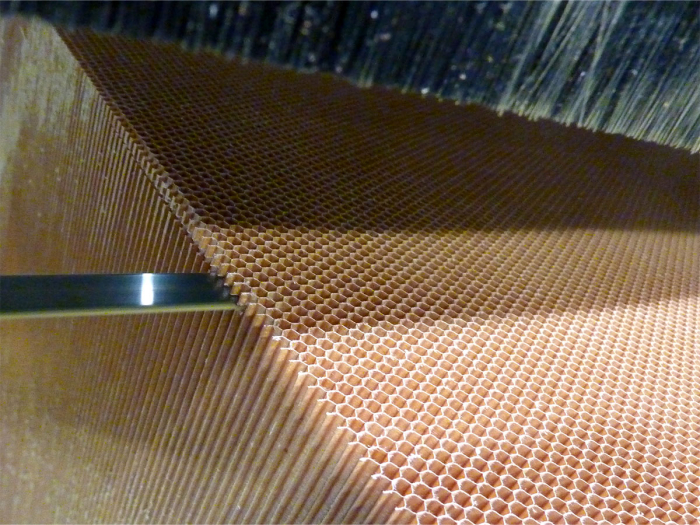
Sawing process – the requirements
Through various cost-intensive processes, these lightweight core materials (be they aramid honeycombs, rigid PET foam, PP honeycombs or balsa wood) are initially used to produce a high-value raw block.
Horizontal sawing is one of the main processes throughout the value chain to produce the end products listed above. To save as much of the high-quality materials as possible during sawing, the focus is on a very thin kerf with a high degree of precision and productivity at the same time: the thinner the kerf, the less raw material is lost during sawing. Special horizontal band saw machines and saw blades are used to produce the above-mentioned components, which fulfil these requirements.
When sawing aramid honeycombs with a cutting width of more than 2 metres using horizontal band saws, customers achieve kerfs smaller than 1 mm, for example, depending on the workpiece type.
To be able to achieve considerable material savings in the long term, every tenth of a millimetre of kerf counts. At the same time, tight thickness tolerances of less than +/- 0.15 mm must be achieved when using extremely thin saw blades.
In addition to the thickness tolerances (in the range of +/- 0.3 mm), the resin up-take is also important when using PET rigid foam panels for rotor blades for wind power plants; this in turn depends on the surface quality after sawing. Different objectives – such as optimum surface quality with high productivity and the thinnest possible kerf – place high demands on the sawing process and on the selection of suitable saw blades.
Sawing process and saw blade – the objectives
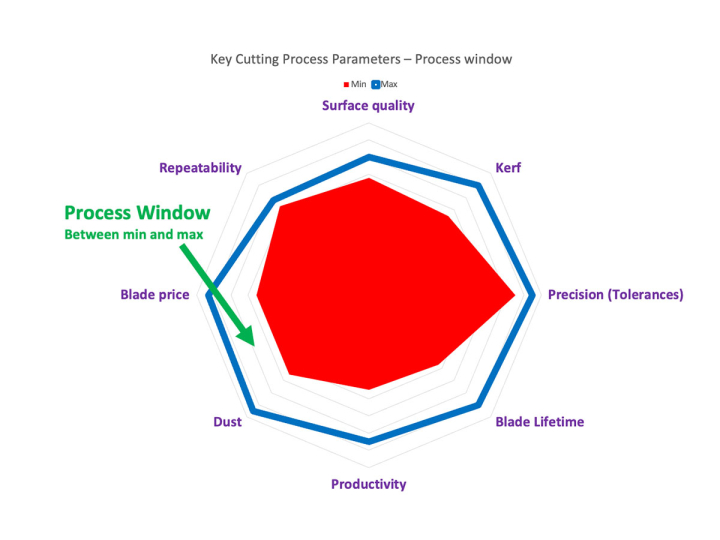
Sawing process and saw blade – the objectives
A range of objectives can be considered in different orders of priority when sawing these lightweight core materials, depending on the application and material. Typical objectives for aramid honeycombs include a high degree of precision in conjunction with very low thickness tolerances of just +/- 0.05 mm. Next comes the requirement for maximum productivity with feed rates of up to 15 m/min for PET rigid foam. Further demands placed on the sawing process include a defined surface quality, e.g., minimal fibres in aramid honeycombs, prevention of scratches and optimised resin uptake in PET and balsa wood. The lowest possible material loss is achieved for example with a thin kerf. Thanks to high precision cutting technology material can also be saved by avoiding a trim cut after each saw blade change. High machine availability due to less saw blade changes, longer lifetime of the saw blade as well as the repeatability of the cutting results are also essential.
Using suitable saw blades with the appropriate cutting parameters plays a crucial role to achieve these objectives. A large range of different process options makes it easier to optimise these targets according to the application and priority.
Suitable saw blades for the respective application are tested in the test centre in collaboration with the customer. Hereby a variety of saw blades are used, from extremely thin saw blades (e.g. thickness of 0.5 mm) to strong bands (e.g. 1.1 mm thickness and widths of up to 34 mm). The types of saw blades varies as well: hardened teeth, bi-metal, stellite-tipped or carbide-tipped teeth, to name just a few examples.
In addition to using the right saw blade, special technologies are used to achieve the targets set out above. These include high-precision, dust-protected, and easily adjustable saw blade guides. Furthermore, it is important to achieve high saw blade speeds of over 4,000 m/min. Intelligent blade tensioning plays as well an essential role: Saw blades are automatically loaded with the calculated clamping pressure by specifying the desired saw blade tension on the control panel. The saw blade is positioned to the desired cutting height with a positioning tolerance of +/- 0.05 mm in a highly precise and dynamic way. Also important is precise workpiece fixing with automatically adjustable vacuum zones depending on workpiece size.
Turnkey solutions including material handling
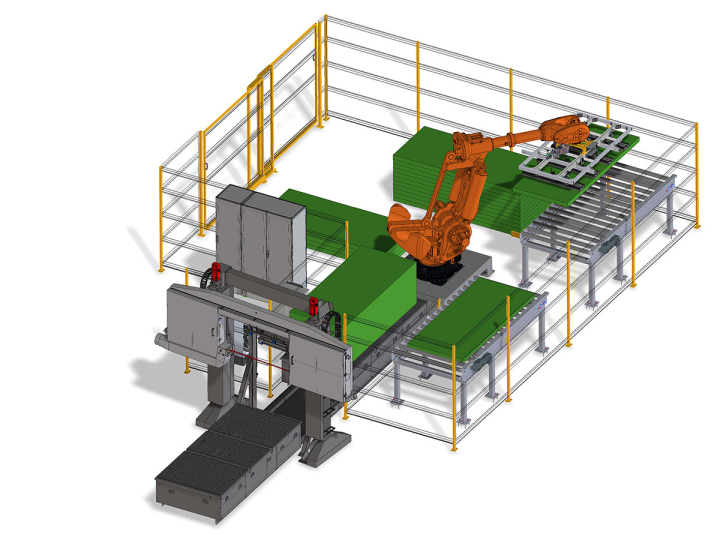
Turnkey solutions including material handling
Bandsaw solutions are often used in which the raw blocks are loaded with a special block handling system and the sawn sheets are removed manually. Increasingly often, however, turnkey solutions are required from a single source, where the block feed to the saw takes place automatically via buffer stations. Afterwards, the sawn sheets are automatically removed by a robot or portal handling and sorted if required. The sheets then run e.g., through the cleaning station and on to quality control (weight, dimensions, ultrasonic testing, etc.), are printed and subsequently stacked. Increasingly often the entire manufacturing process is being carried out using a complete production line manufactured from a single source.
Digitising the sawing process – "the Digital Cockpit"
Digitally depicting the sawing process also maximises productivity. Band saw operation is monitored with various apps and supported by subsequent data analysis. This takes place both with the help of real-time data and based on aggregated historical data, which is stored continuously.
The monitoring app records such data as for example axis speeds and current power consumption of drive axes, as well as position data from machine axes and much more. Each data record can be limited with target and actual values – if a value exceeds a predefined limit, a corresponding alarm is generated via the alarm app. Production management can then intervene immediately and analyse the anomaly.
Heermann Maschinenbau GmbH – HEMA
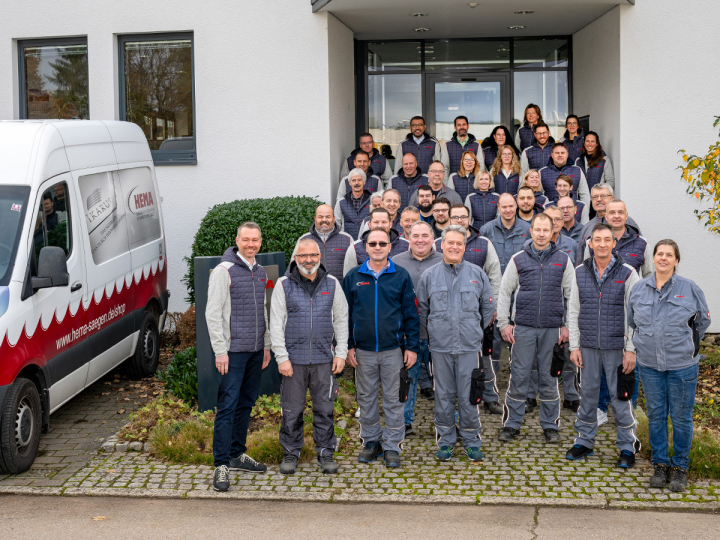
HEMA, a company with over 100 years of experience, develops, manufactures, and distributes band sawing systems and cutting solutions for different materials and applications. A particular specialisation of the HEMA portfolio is solutions for cutting lightweight materials, as well as construction and insulation materials. The company supplies band saw and cutting solutions ranging from single machines to complete block processing lines including loading, sawing, trimming, handling, transporting, sanding, etc. The focus is on flexible, high-precision customer-specific solutions. HEMA exports to Europe, the USA and Asia, with an export ratio of over 90%.
HEMA has belonged to the Austrian Wintersteiger Group since January 2022. With Wintersteiger Sägen GmbH in Arnstadt, Thuringia, the development and production of saw blades are carried out within the group. Automation expert VAP-Wintersteiger GmbH in Mettmach, Austria – with over 20 years of experience in the automation of production lines – is also on board. Like Wintersteiger, HEMA is also a specialist, technology and quality leader in a niche sector.
Heermann Maschinenbau GmbH
72636 Frickenhausen / Germany