15.07.2020
"Fully-automatic timber cosmetics" at Scheucher Holzindustrie
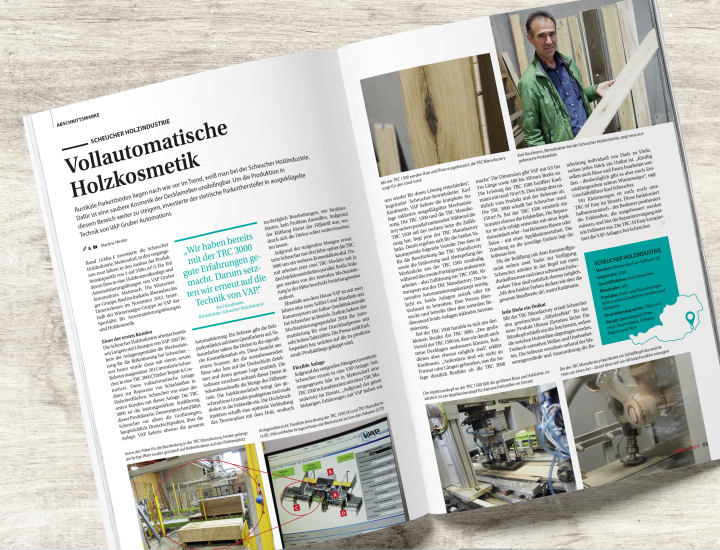
Report by Martina Nöstler, published in Holzkurier on 07/21/2020
Scheucher Holzindustrie knows that rustic parquet flooring is still on trend. So, a clean cosmetic appearance on the top layers is essential. To further increase production in this area, the Styrian parquet manufacturer has invested in sophisticated technology from VAP Gruber Automations.
Scheucher Holzindustrie, Mettersdorf, invested around €14 million over the last two years with the aim of extending production capacity from 2 to 3 million m2/year. Part of this was used for a timber cosmetics system and automation solutions from VAP Gruber Automations, Mettmach. The WINTERSTEIGER group, based in Ried im Innkreis, acquired the company in November 2012. Within the WINTERSTEIGER Group, VAP is the specialist in automation solutions and timber cosmetics.
SHARE:
One of the first customers.
Scheucher Holzindustrie has been working with solutions from VAP for many years: In 2007, the system specialist created the mechanization for briquetting at Scheucher – and this year it was equipped with a new robot. In 2011, Scheucher invested in a TRC 3000 (Timber Repair & Cosmetics). This fully-automatic system is used to repair defects in wood surfaces. Scheucher was one of the first customers with this system. The TRC 3000 is the most powerful version in this product range. Thus, Scheucher mainly runs large volumes, mainly three-layer parquet, through the system. VAP also supplies all the automation: One robot passes the raw parquet floorboards to a cross conveyor. Vacuum lifters feed the boards into the actual cosmetic station. This consists of a scanner, which detects the cracks or knots to be repaired on the top layer and determines their exact position. The software uses this data to calculate the amount of filling material in a matter of seconds. The injection unit precisely injects the exact dose of melted granulate into the defect. The high-pressure injection creates an optimum connection between the thermoplastic and the wood, so that subsequent processing such as textured brushing is no problem. The filling material hardens as it cools, allowing the boards to be processed right away.
Due to the rising volumes, Scheucher added another cosmetic module to the TRC 3000 just three years later. So now, two TRC modules each with three injection units work in parallel. Both systems are fed/emptied by the central mechanism in the middle. Scheucher has also been using a new VAP sanding and brushing line with camera system for inline quality control for two years now. In 2018, the mechanization specialist also supplied the automation for a throughfeed press with very fast cycles. The press manufactures endless parquet, which is cut to the required product length.
"We have been very pleased with the TRC 3000 to date. Which is why we have opted for technology from VAP once again," says Karl Kaufmann, Operations Manager at Scheucher Holzindustrie.
Flexible system.
Scheucher invested in another VAP system to handle rising volumes: As of last year, a TRC 1500 has been used in Mettersdorf in conjunction with a TRC Manufactory. "We opted for another VAP solution as we've been very pleased with VAP to date," explains Scheucher's Operations Manager Karl Kaufmann. VAP supplied the entire system including the sophisticated mechanization. The TRC 1500 and the TRC Manufactory are positioned parallel with one another. While the TRC 1500 has a feed on the right-hand side, the TRC Manufactory's feed is on the left. This results in the following advantages for the two vacuum gantries: One feeds the TRC Manufactory and empties and destacks the workpieces from the TRC 1500, while the other gantry does the reverse – it feeds the TRC 1500 and transports items out of the TRC Manufactory. The innovative automation concept enables both systems to operate as stand-alone systems or in combination. One person monitors and operates both systems, including automation via the central operator platform. The TRC 1500 is the TRC 3000's little brother.
"The major advantage of the TRC 1500 is that we can repair pure top layers, but raw planks are also possible," explains Kaufmann. "What's more, we're not tied to formats or lengths, which makes the system much more flexible than the TRC 3000." VAP specifies the dimensions as 0.5 to 3 m long and 100 to 350 mm wide. Kaufmann estimates that the TRC 1500 achieves around 70 m2/h – depending on the product and raw material. At Scheucher, the TRC 3000 delivers around 150 m2/h. The TRC 1500 also features a scanner which detects defects. The repair itself is either carried out by an injection unit or – in the case of smaller cracks or knots – with an application unit. The software determines which unit carries out the work. Two tanks are available for filling with plastic granulate. Scheucher normally works with a dark brown and a black color – but other colors are possible too. "We can cover a wide range with these two colors though," says Kaufmann.
Each floorboard is unique.
Scheucher uses the TRC Manufactory to achieve the desired 'rustic look' for its new product Ufenau Elevation oak: A brush head grinds around the knot to remove the soft wood areas. This creates waves and unevenness. The software calculates the processing individually for each board based on the grain and knot arrangement, so that each piece is unique. "In future, cracks and chamfers are to be processed too – but there is still some engineering work to be done by WINTERSTEIGER in this regard," says CEO Karl Scheucher. A TRC-M Easy is also used for small volumes. This is semi-automatic – the operator positions the defects that need to be repaired and triggers the repair process via a foot switch. The TRC-M Easy rounds off the VAP systems at Scheucher.
- Location: Mettersdorf am Saßbach (2)
- Founded: 1920
- CEO: Karl Scheucher
- Employees: 245
- Products: Two and three-layer parquet in a range of sizes and wood types
- Production capacity: 3 million m2/year
- Sales: Mainly Austria, Germany, Switzerland, around 70 % exports