10-04-2022
A thin-cutting band saw expands to form a plant
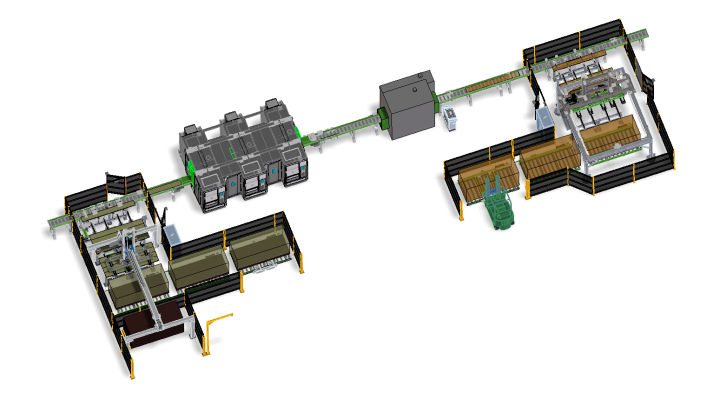
WINTERSTEIGER Area Sales Manager Gerald Dallinger is seeing an increasing number of inquiries regarding the DSB Twinhead Pro XM thin-cutting band saw – with a preference for the set of three. He explains the reasoning behind this exciting development in an interview.
Customers are increasingly inquiring about the DSB Twinhead Pro XM thin-cutting band saw (two saw modules) with several machines connected in series. Where is this trend toward size coming from?
For one thing, customers want to optimize their processes. With several band saws connected in series, the wooden block no longer has additional material handling to complete the cutting process. Ideally, it only travels through the plant once. If a company is large enough and needs more capacity, it makes sense to operate several machines in series.
What is made even more efficient with a large band saw plant?
The cutting of wet lamellae is also possible on the DSB Twinhead Pro XM. Wet cutting is becoming increasingly popular, as drying the wood is faster and more efficient: a 30 cm thick wooden block needs approximately 2 to 3 months for drying; thin lamellae are finished in 1 to 2 days. This is also a question of capital commitment, as the raw material for dry cutting must be pre-financed over several months.
SHARE:
Are there additional advantages?
Yes, in terms of quality. Wet cutting with subsequent drying leads to less discoloring on the lamella, for example due to the sugar content of oak, where white stripes can appear in the wooden block. This hardly ever occurs during wet cutting. Moreover, the trend toward single-plank flooring is set to continue: the lamellae are wider and longer and are much easier to cut with the band saw than with the frame saw. Knotholes also cause fewer problems with band saw technology.
Do you generally recommend band saws over frame saws?
Never! Frame saws certainly have their uses. The band saw is no longer economical during wet cutting for certain formats and applications, for example if the top layer is thinner.
Is there an ideal plant size in terms of cost-effectiveness?
With the DSB Singlehead NG XM and DSB Compact NG XM band saws, we were able to connect up to six machines in series. However, the input material must then already be extremely thick for this to be economically viable. Nevertheless, strong wooden blocks of this type also have more tension, which in turn leads to inaccuracies during cutting and to timber yield losses.
A sawing line with three machines has proven ideal for many projects. With VAP-WINTERSTEIGER's automation expertise, we are able to deliver complete sawing lines. At the start of the plant is a cross conveyer with block separation, a roller conveyer leads to the planer or moulder (not from WINTERSTEIGER), and then to the cutting line with three DSB Twinhead Pro XM machines. At the end of the plant is a cross conveyor which transfers the finished lamellae to the retrieval point where piles are formed.
Can individual band saw machines also be expanded to form a plant?
The DSB Twinhead Pro XM and DSB Singlehead NG XM can be expanded at any time - machine by machine. The multiple saws operate as one, just as before and with a sophisticated operating concept. The entire plant can be controlled from any machine and each individual machine remains fully accessible for cleaning or maintenance purposes.
If you are interested, please contact your Area Sales Manager – they will be happy to help!