DSB Singlehead Pro XM
Thin-cutting band saw
DSB Singlehead Pro XM Thin-cutting band saw
Uncompromisingly versatile
DSB Singlehead Pro XM Thin-cutting band saw
Uncompromisingly versatile
The all-rounder in thin-cutting technology
If you need maximum flexibility for changing requirements, the DSB Singlehead Pro XM is the perfect choice. Numerous features enable you to cut wood even under the toughest conditions – regardless of the wood type and application. With flexible operation and unrivaled performance, it offers maximum precision and efficiency.
Thanks to the machine’s ingenious design, the capacity can be expanded retrospectively with ease: The band saw can be easily expanded to include up to six machines, offering maximum flexibility. The robust design plus WINTERSTEIGER’s decades of expertise guarantee optimal machine availability and fast amortization.
- Robust block guide: For a wide range of applications and precision wood guidance.
- High-tech saw control: For maximum precision and optimum cutting quality.
- Maximum flexibility and efficiency: Adaptable to different production requirements.
- Automatic tensioning device: For fast and safe saw blade changes.
- Integrated cooling system: For a longer saw blade service life.
- User-friendly control: With touchscreen interface for easy operation.
Your benefits summed up
Efficient operation
- Easy to operate
- Versatile use
- Increased drive power
- Intelligent sensor technology
Overview of the cutting process
- Automatic block width measurement
- Automatic bearing monitoring for preventive replacement
- 12-inch multi-touch display for optimum usability
Uncompromisingly versatile
- Continuous, solid supporting table with special coating
- Processing of any block characteristics
- Robust design for the toughest applications
High-tech saw control for optimal precision
- Gentle saw blade entry for better cutting performance
- Sensor-controlled saw monitoring
- High-tech carbon guides
- Band tracking control
Maximum flexibility and efficiency
- Optimized for wet and dry cutting
- Whether you have a stand-alone machine or 6 machines in-line: Your machine grows with you!
Minimal kerf – maximum profit.
Those who want to remain successful in the future must keep a firm hand on conserving material in these times of raw material shortages and subsequent high prices, as this trend will only become more prevalent going forward. Fortunately, conserving material is a specialty of the DSB Singlehead Pro XM. WINTERSTEIGER promises minimal kerf, paired with maximum precision. This allows an increase in timber yield of up to 40 % compared to conventional wood-cutting methods.
Your gain:
up to 40 % greater timber yield!
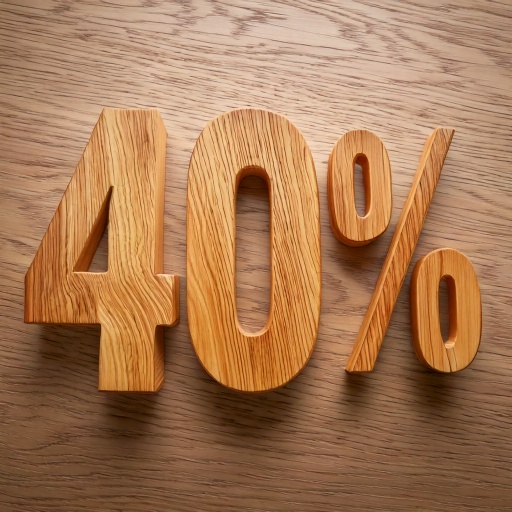
Regular cutting with increased loss caused by a lack of precision.
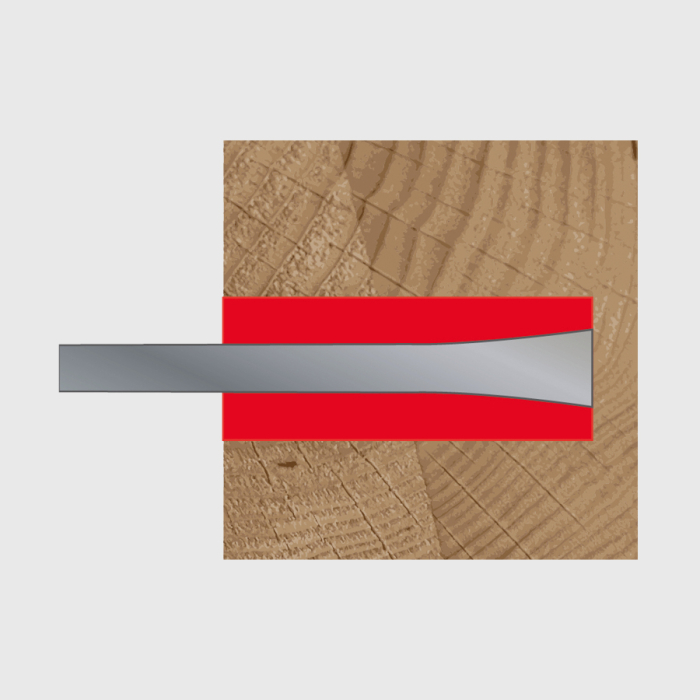
WINTERSTEIGER thin cutting with minimal cutting loss and maximum precision!
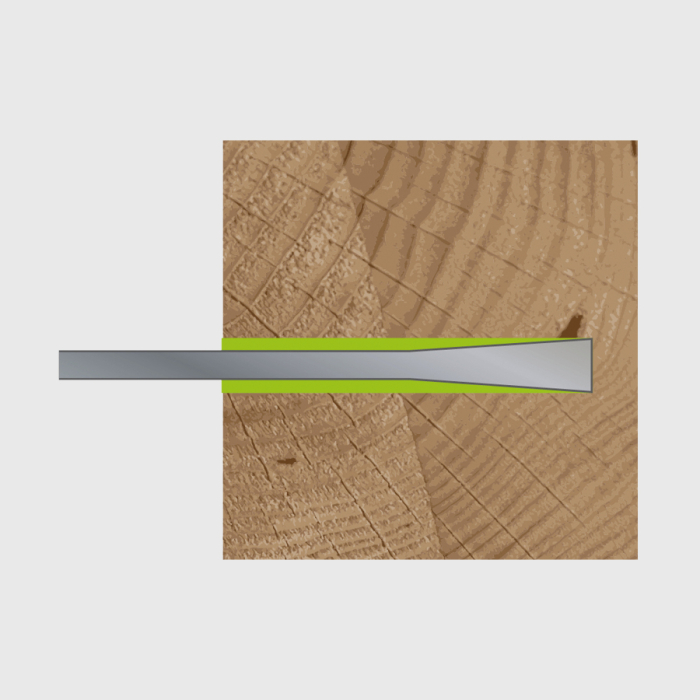
Lamella thicknesses from 1.3 mm.
The highly innovative combination of thin saw band and precise saw band and rigid block guide enables the production of extremely thin lamellas. With this outstanding technical achievement, the DSB Singlehead Pro XM closes the gap between classic veneer and high-quality sawn veneer.
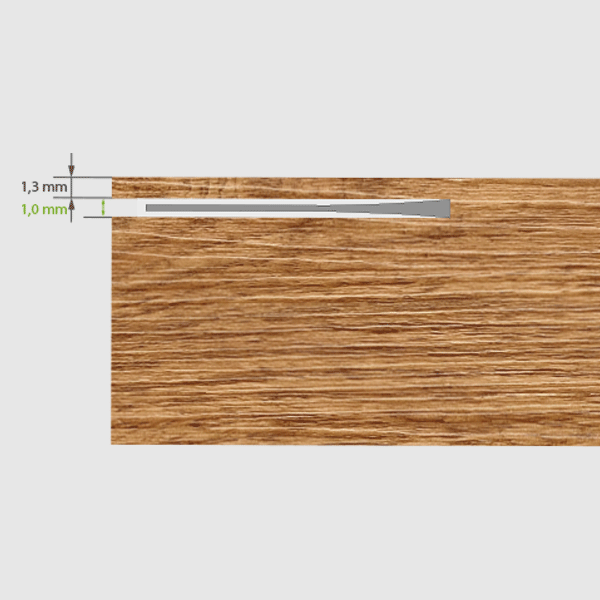
Robust block guide for a wide range of applications.
Innovative feed system.
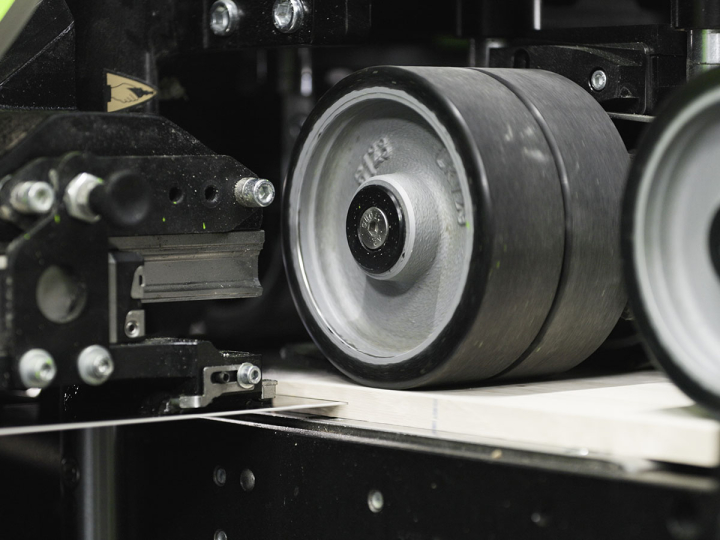
Driven transport rollers above and below guarantee continuous block feeding, even when faced with extreme workpiece characteristics. The specially rubberized transport rollers and the innovative counter-pressure system guarantee optimum grip as well as minimum friction for wet or dry material. The specially coated supporting table simultaneously ensures that the workpiece is as stable as possible. The transport rollers are electronically controlled and infinitely adjustable at the charging and discharging unit (4–20 m/min). The vertical stabilization of the workpiece in the cutting area is the basis for the perfectly precise cut.
The DSB Singlehead Pro XM owes its unusually high level of precision to the specially coated supporting table. Additional driven pressure rollers immediately above the cutting area guarantee the constant stability of the workpiece across its full width. This gives you the ability to cut not only pre-planed material, but also uneven and rough-cut blocks with longitudinal or latitudinal deformations or that are cupped or torsion-warped.
Optimal feed for every application.
For high performance requirements in the highest capacity range, the DSB Singlehead Pro XM features a feed rate specifically for high-speed applications; for example, an optional feed rate with a range of 8 to 45 m/min is available for processing softwood.
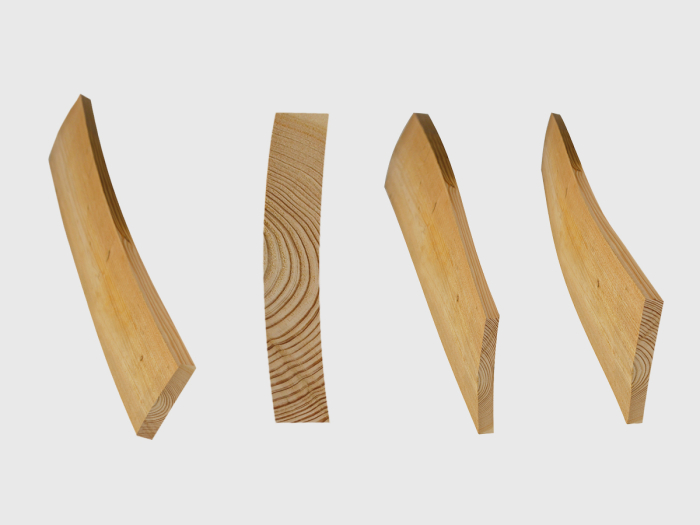
Wooden blocks with longitudinal/latitudinal deformation, cupped or torsion-warped
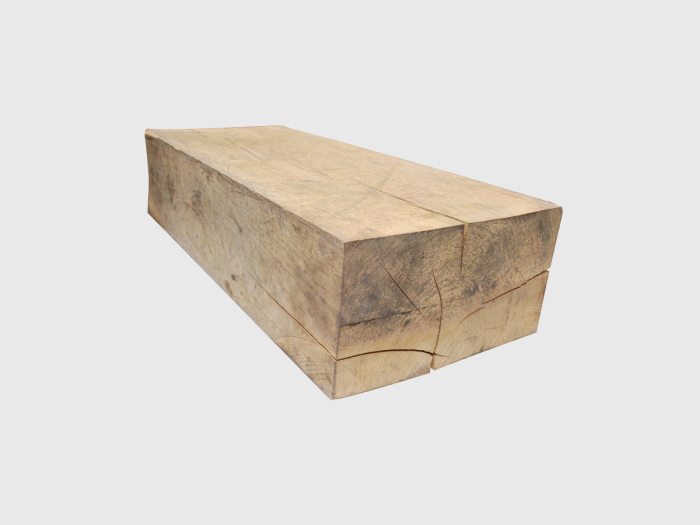
Wooden block dry cutting
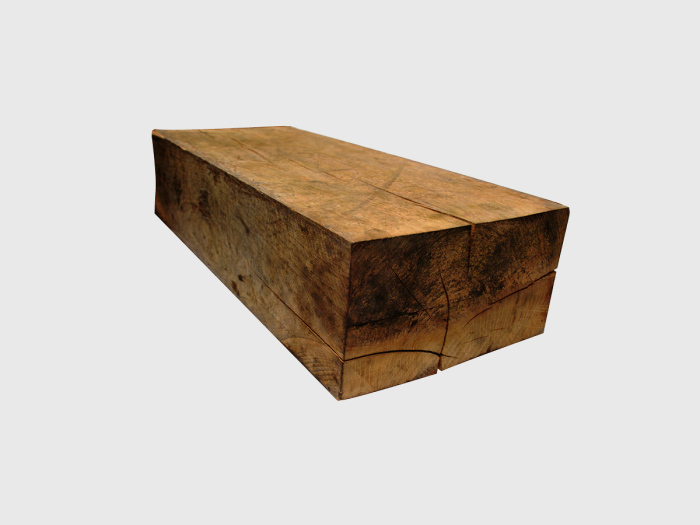
Wooden block wet cutting
Attribute |
Singlehead 350 Pro |
Singlehead 530 Pro |
Singlehead 660 Pro |
Main drive nominal capacity |
32 kW |
37 kW |
37 kW |
Saw band speed, infinitely adjustable |
Up to 60 m/sec |
Up to 50 m/sec |
Up to 50 m/sec |
Feed speed 1) |
1–18 m/min |
1–18 m/min |
1–18 m/min |
Saw band guide |
Carbon guide, adjustable on one side |
Carbon guide, adjustable on one side |
Carbon guide, adjustable on one side |
Min. / max. block width |
30 mm / 350 mm |
30 mm / 530 mm |
30 mm / 660 mm |
Min. / max. block height |
5 mm / 165 mm |
5 mm / 165 mm |
5 mm / 165 mm |
Min. / max. block length |
350 mm / unlimited |
350 mm / unlimited |
350 mm / unlimited |
Max. cutting width |
350 mm |
530 mm |
660 mm |
Lamella thickness min. 1) |
1.5 mm |
1.5 mm |
1.5 mm |
Cutting accuracy 1) |
Approx. +/- 0.15 mm |
Approx. +/- 0.15 mm |
Approx. +/- 0.20 mm |
Kerf |
From 1.1 mm |
From 1.1 mm |
From 1.1 mm |
More power
Fast positioning
The servo-driven module adjustment via precision threaded spindles allows up to 10 x faster height adjustment. You therefore achieve quick and optimum utilization of the cutting height.
High drive power
With the DSB Singlehead Pro, 37 kilowatts of drive power ensure a high cutting performance with sufficient reserves, even for demanding applications.
Chip auger and suction unit
Powerful chip removal
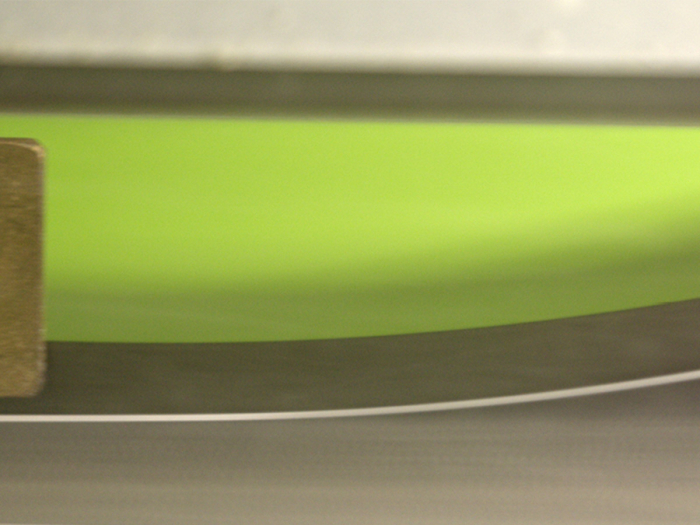
The machine’s suction unit is designed so that chips are removed from the machine as quickly and efficiently as possible. This prevents temperatures from becoming too high inside the machine. Primarily in the softwood segment and at high feed speeds, where more chips accumulate in a shorter time, optimized extraction is a clear benefit.
Discharge auger
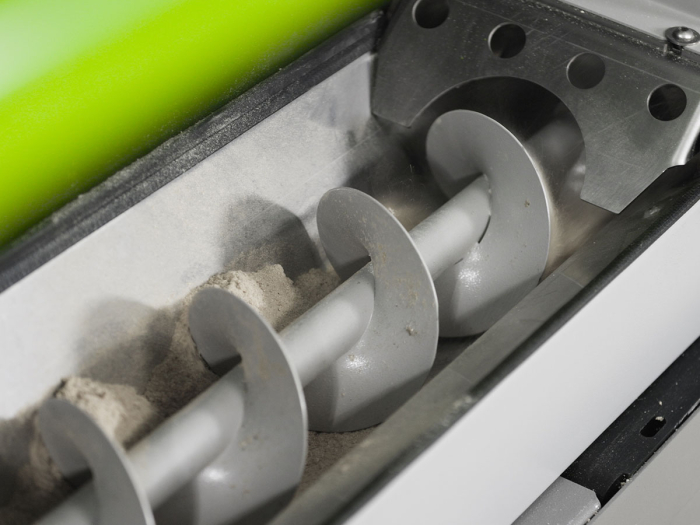
The tried-and-tested discharge auger is now also used in the DSB Singlehead Pro XM, the largest machine in our product portfolio. It ensures that chips are continually removed from the machine interior. It also provides support during machine cleaning: Chips can easily be swept into the discharge auger.
High-tech saw control for optimal precision.
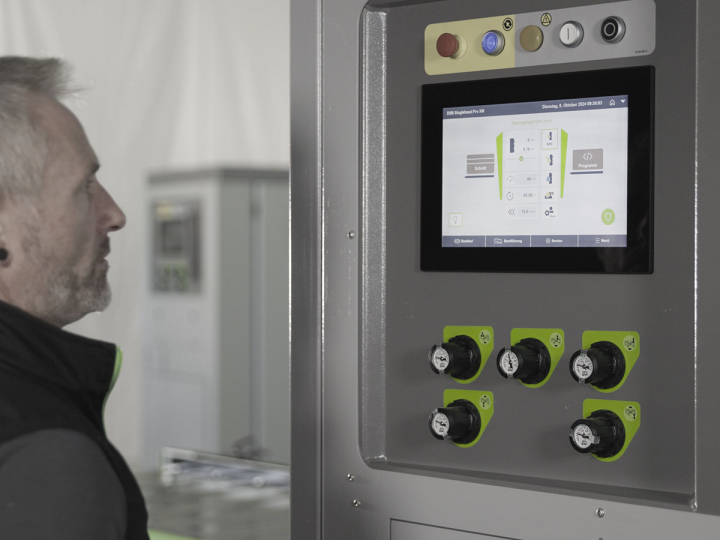
Gentle saw blade entry for improved cutting performance.
The smooth cutting system protects the saw and increases the quality of the output. Thanks to the reduced speed at entry of the saw into the wooden block, the forces working on the saw are minimized: The deflection of the blade is reduced. Once the saw is completely submerged in the wooden block, the feed speed is increased again.
Sensor-controlled saw monitoring.
Sensors monitor the force on the saw blade guide and the distance between the saw blade and saw blade guide. Continuous monitoring of the saw blade and saw blade guide allows the operator to keep the cutting process under control: The machine automatically prevents production errors with freely adjustable threshold values for the force and position of the saw blade.
Your benefits:
- Saw blade protection:
A loss of tension on the saw blade through overstretching is prevented. - Machine protection:
The machine components are protected because the feed or the machine is stopped when the saw drifts.
- Material protection:
Saw blade drift is detected early, preventing tolerances from being exceeded and reducing waste. - Tool costs:
The graphic display allows proactive retooling at precisely the right time.
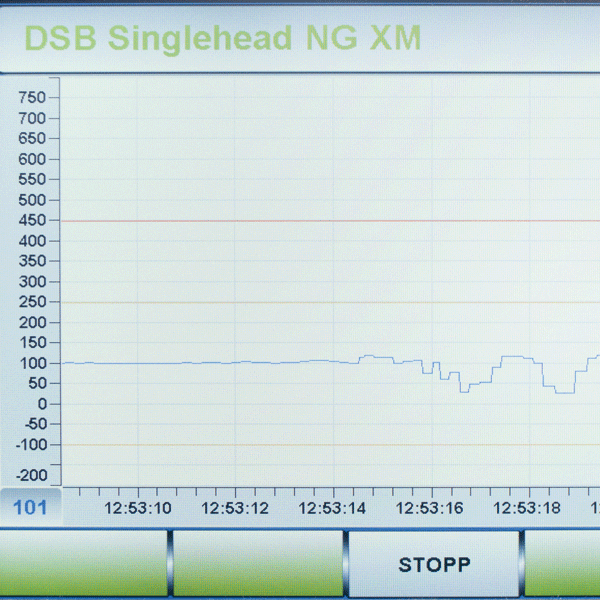
Sensor-controlled saw monitoring
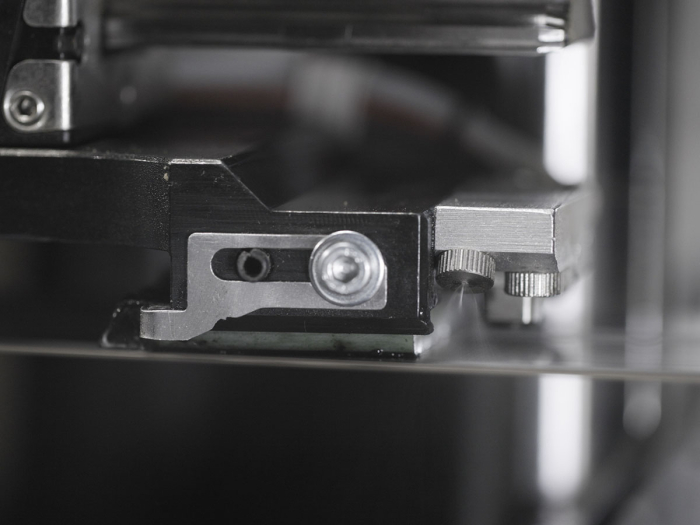
High-tech carbon guides.
This high-tech composite material made of abrasion-proof carbon fibers and heat-resistant epoxy resin guarantees precise band guiding and an extremely long lifetime.
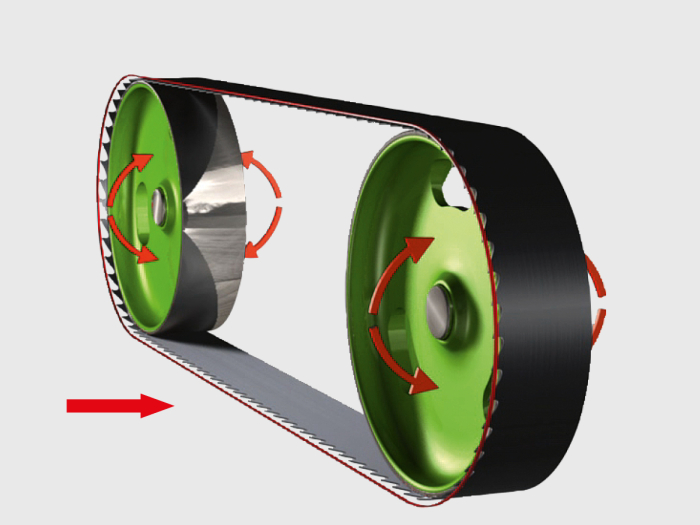
Automatic band tracking control.
When cutting non-homogeneous materials such as wood, the saw band is exposed to different cutting forces. The automatic band tracking control uses a sensor to detect the displacement of the saw band caused by differences in cutting force. An adjusting mechanism driven by an electromotor controls the deflection pulleys and guarantees optimum positioning of the saw band. This prevents the saw band running off the deflection pulley.
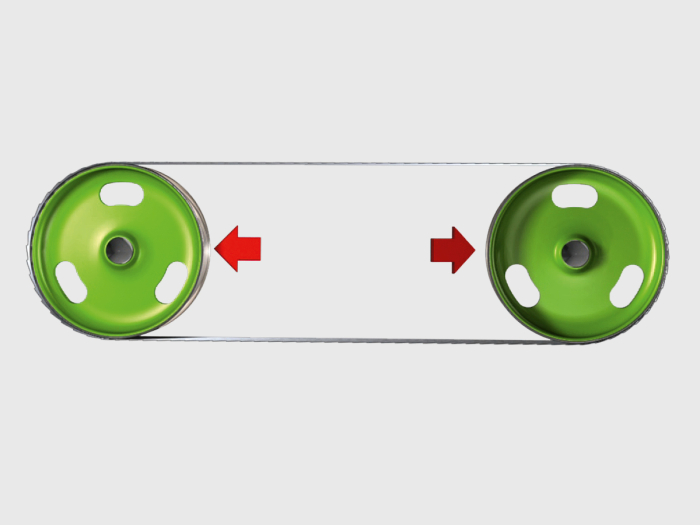
Servopneumatic saw band tensioning.
A servo valve controls the saw blade tension, which is adjusted to match the saw blade dimensions. During breaks in operation, the clamping pressure is reduced, which helps to protect the saw band.
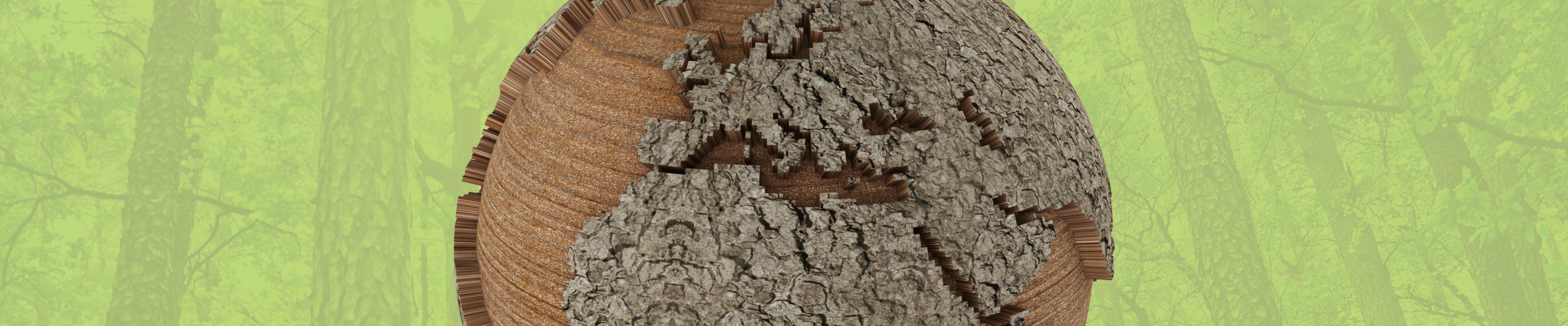
World of Woodtech
WINTERSTEIGER gives you the choice: We will transform your machine into an automated production system.
Maximum flexibility and efficiency.
Optimized for wet and dry cutting.
Flexibility means being equipped for any demands and the challenges they bring. Whether it is the cutting width, maximum block height of 165 mm, or the innovative spraying system – everything about the DSB Singlehead Pro XM is geared toward flexibility.
Clear and straightforward with a practical wood program.
The clear user interface allows all desired parameters to be set quickly and easily. From apprentices to experts, the user guidance can be understood by anyone. All important settings can be applied clearly on the start screen.
Practical: The software features a practical memory function for commonly recurring process parameters. It also boasts multilingual user guidance and a range of service and help menus. These include cutting, timber, and sawing programs, operating data acquisition, and diagnostic and maintenance displays.
Lubrication, cooling, cleaning as required
Innovative spraying system with up to two different lubricants to lubricate and cool the saw band and prevent resin deposits, thereby increasing the service life of the saw blades.
An additional spraying system with water is optionally available for cutting wet wood.
Intuitive operation
Display size: 12”
Smartphone-quality operation
Clear and straightforward with a practical wood program.
The clear user interface allows all desired parameters to be set quickly and easily. From apprentices to experts, the user guidance can be understood by anyone.
From an individual machine to a multi-module production system.
DSB Singlehead Pro XM – a machine concept that grows with your capacity requirements. You start with an individual thin-cutting band saw and expand as required into a complete production system with up to 6 machines. The production systems form complete manufacturing units in a compact design.
Automation and integration into individual process solutions are part of WINTERSTEIGER’s core competence.
Saw blades developed and produced by Wintersteiger itself.
Customers with exacting requirements require individual tools.
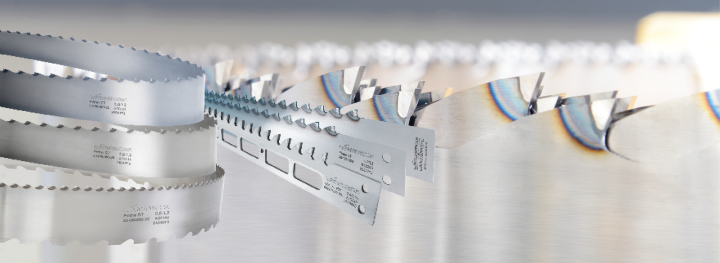
WINTERSTEIGER supplies the best material, optimum saw blade dimensions, and tooth geometries in line with requirements.
Thin-cutting systems and band saws from WINTERSTEIGER are impressive!
- Optimum solution
- Maximum cost-effectiveness
- Reliable partner:
Customer-specific complete systems
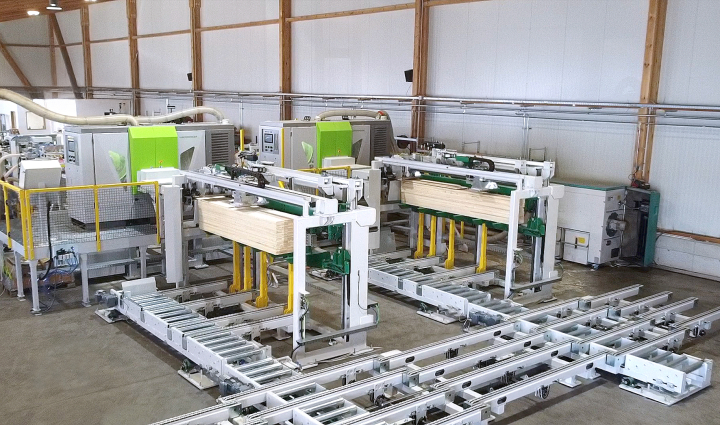
Customer-specific complete systems
Within the WINTERSTEIGER Group, VAP-WINTERSTEIGER is the plant engineering and automation specialist. Renowned manufacturers from all over the world swear by our “MADE IN AUSTRIA” systems.
Softwood production line for multilayer boards. On this fully automated plant, blocks are thickness-planed, timber is cut into top layers by 3 DSB Singlehead Pro XM thin-cutting band saws connected in series, the top layer stack is planed on the sides, lamellas are separated and cleaned of dust, and the top layers are quality assessed, all for the production of multilayer boards.
WINTERSTEIGER after-sales service.
When the delivery ends the support begins.
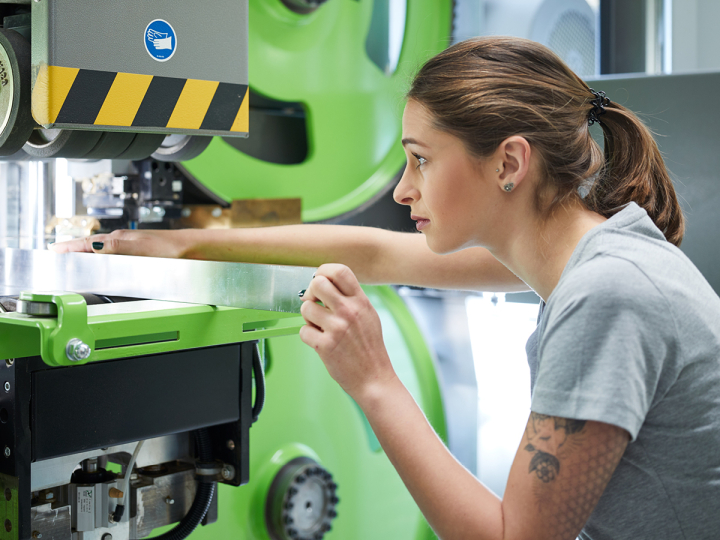
WINTERSTEIGER after-sales service.
When the delivery ends the support begins.
The best time to evaluate the quality of an investment is several years after delivery. For this reason, WINTERSTEIGER has an after-sales service that is available to you all over the world.
- Commissioning and training
- Production support
- Proactive maintenance
- Blanket orders for consumables and saws
- On-call help desk.
WINTERSTEIGER’s experienced sales staff can help tailor an individual solution to fit your needs!